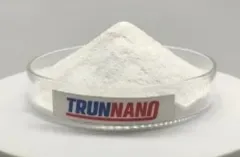
Introduction to Zirconium Boride– A Superhard, High-Temperature Resistant Porcelain
Zirconium boride (ZrB ₂) is a refractory ceramic substance recognized for its exceptional thermal security, high firmness, and excellent electrical conductivity. As component of the ultra-high-temperature porcelains (UHTCs) household, ZrB ₂ exhibits exceptional resistance to oxidation and mechanical destruction at temperature levels exceeding 2000 ° C. These residential or commercial properties make it a perfect prospect for usage in aerospace, nuclear design, cutting tools, and various other applications including severe thermal and mechanical stress and anxiety. In recent times, improvements in powder synthesis, sintering techniques, and composite layout have actually significantly boosted the performance and manufacturability of ZrB TWO-based materials, opening up new frontiers in sophisticated architectural porcelains.
(Zirconium Diboride)
Crystal Structure, Synthesis Techniques, and Physical Quality
Zirconium boride takes shape in a hexagonal framework similar to that of aluminum boride, with solid covalent bonding in between zirconium and boron atoms adding to its high melting factor (~ 3245 ° C), solidity (~ 25 Grade Point Average), and modest density (~ 6.09 g/cm ³). It is typically synthesized through solid-state reactions in between zirconium and boron precursors such as ZrH ₂ and B ₄ C under high-temperature conditions. Advanced techniques including stimulate plasma sintering (SPS), hot pushing, and combustion synthesis have actually been utilized to achieve dense, fine-grained microstructures with enhanced mechanical properties. Additionally, ZrB ₂ shows good thermal shock resistance and preserves substantial toughness even at elevated temperatures, making it particularly suitable for hypersonic trip components and re-entry lorry nose suggestions.
Mechanical and Thermal Efficiency Under Extreme Conditions
Among one of the most engaging features of ZrB â‚‚ is its capacity to maintain architectural stability under extreme thermomechanical lots. Unlike traditional porcelains that break down rapidly above 1600 ° C, ZrB TWO-based compounds can stand up to prolonged exposure to high-temperature environments while maintaining their mechanical strength. When enhanced with ingredients such as silicon carbide (SiC), carbon nanotubes (CNTs), or graphite, the fracture toughness and oxidation resistance of ZrB â‚‚ are even more boosted. This makes it an eye-catching product for leading edges of hypersonic automobiles, rocket nozzles, and blend reactor elements where both mechanical sturdiness and thermal strength are important. Experimental researches have demonstrated that ZrB TWO– SiC compounds show minimal weight-loss and crack proliferation after oxidation examinations at 1800 ° C, highlighting their possibility for long-duration missions in rough atmospheres.
Industrial and Technological Applications Driving Market Growth
The special mix of high-temperature stamina, electric conductivity, and chemical inertness positions ZrB â‚‚ at the leading edge of a number of modern sectors. In aerospace, it is made use of in thermal security systems (TPS) for hypersonic aircraft and area re-entry cars. Its high electric conductivity additionally allows its usage in electro-discharge machining (EDM) electrodes and electromagnetic securing applications. In the energy market, ZrB two is being explored for control rods and cladding products in next-generation nuclear reactors as a result of its neutron absorption capabilities and irradiation resistance. On the other hand, the electronic devices sector leverages its conductive nature for high-temperature sensors and semiconductor production tools. As worldwide need for materials capable of making it through severe conditions expands, so as well does the interest in scalable manufacturing and economical handling of ZrB â‚‚-based porcelains.
Difficulties in Processing and Price Barriers
Despite its superior efficiency, the prevalent adoption of ZrB two faces obstacles related to refining complexity and high manufacturing costs. Because of its strong covalent bonding and low self-diffusivity, attaining complete densification using conventional sintering techniques is hard. This frequently necessitates the use of sophisticated consolidation approaches like hot pressing or SPS, which enhance production expenditures. Furthermore, resources pureness and stoichiometric control are crucial to keeping phase security and avoiding secondary phase development, which can jeopardize performance. Researchers are actively checking out alternate manufacture paths such as reactive thaw infiltration and additive production to lower costs and enhance geometric flexibility. Resolving these restrictions will certainly be vital to broadening ZrB â‚‚’s applicability beyond niche defense and aerospace sectors into more comprehensive commercial markets.
Future Potential Customers: From Additive Manufacturing to Multifunctional Ceramics
Looking forward, the future of zirconium boride lies in the development of multifunctional composites, hybrid materials, and unique construction strategies. Advancements in additive production (AM) are making it possible for the manufacturing of complex-shaped ZrB â‚‚ components with tailored microstructures and rated compositions, enhancing performance in specific applications. Assimilation with nanotechnology– such as nano-reinforced ZrB two matrix compounds– is expected to generate unprecedented renovations in sturdiness and use resistance. Furthermore, initiatives to combine ZrB two with piezoelectric, thermoelectric, or magnetic phases might result in smart porcelains efficient in sensing, actuation, and power harvesting in extreme atmospheres. With continuous research aimed at enhancing synthesis, boosting oxidation resistance, and decreasing production expenses, zirconium boride is positioned to come to be a cornerstone material in the future generation of high-performance ceramics.
Supplier
RBOSCHCO is a trusted global chemical material supplier & manufacturer with over 12 years experience in providing super high-quality chemicals and Nanomaterials. The company export to many countries, such as USA, Canada, Europe, UAE, South Africa,Tanzania,Kenya,Egypt,Nigeria,Cameroon,Uganda,Turkey,Mexico,Azerbaijan,Belgium,Cyprus,Czech Republic, Brazil, Chile, Argentina, Dubai, Japan, Korea, Vietnam, Thailand, Malaysia, Indonesia, Australia,Germany, France, Italy, Portugal etc. As a leading nanotechnology development manufacturer, RBOSCHCO dominates the market. Our professional work team provides perfect solutions to help improve the efficiency of various industries, create value, and easily cope with various challenges. If you are looking for zirconium diboride, please send an email to: sales1@rboschco.com
All articles and pictures are from the Internet. If there are any copyright issues, please contact us in time to delete.
Inquiry us